Engineer building softer, quieter, more human robots
12 February 2025
Bryan Ruddy’s first foray into robots came through fight-to-the-death BattleBot combat. Now he builds robots designed to help people live better lives
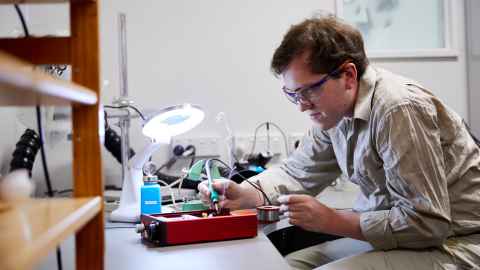
Dr Bryan Ruddy was a mechanical engineering postgraduate student at MIT in Boston when a bunch of nerdy mates persuaded him into the arena - the robot combat arena.
BattleBot aficionados built super-strong remote-controlled robots, which fought in live events and on TV. BattleBots is still going - a team led by University of Auckland engineering alumni won the 2020 world competition.
Back in the 2000s, Ruddy began to realise some of the scientific, research and design work going into BattleBots was cutting edge. There had to be a PhD in there, he thought.
“I realised that you can do a lot more with an electric motor than a standard design allows, and started building my own motors to push those limits. I changed my PhD topic, started formally researching it, and it has led to an interesting career.”
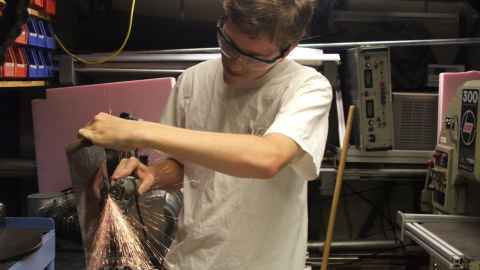
A couple of decades on, now in New Zealand and working with the Auckland Bioengineering Institute at the University of Auckland, Ruddy's work is still about building better robots, particularly for use in health – stroke rehabilitation, for example.
A recent project involves building a robotic device which can help move the ‘bad’ arm of someone who has had a stroke.
“One of the biggest problems after a stroke is patients have much more difficulty using one side of their body than the other, and so they don’t use it. Their muscles waste away, and even though their brain can recover, their body has changed and this can make the disability permanent.
“Our robot helps hold up the patient’s arm, supporting the weight and making it easier to use the stroke-affected side. To make the robot simple and light, it uses a custom-built linear motor that goes between the hip and the arm, which can provide force to help provide support without forcing the arm to be in a particular position.
“We’ve tested the robot out on healthy volunteers, and are hoping to try it with stroke patients soon.”
If a motor isn’t as good as our muscles, why don’t we make robots like our muscles?
Ruddy says one of the biggest problems with robots is that compared to humans, they’re weak and clumsy.
“That’s because the motors used to drive them aren’t good enough, especially when they move slowly - like people do.”
So he and his team are taking inspiration for their robots from biology. The stroke rehabilitation robot works with a piston-like linear motor, which extends and shortens, doesn’t have gears, and is much quieter than a normal motor.
“If a motor isn’t as good as our muscles, why don’t we make robots like our muscles?”
Another problem with robots is they are hard and heavy; if you accidentally whack yourself, or someone else, with an exoskeletal arm assistance robot you could do some real damage.
Which is why he is also working on a project that involves using liquid metals to make soft robots.
“Instead of stiff metal and plastic parts, a robot made of soft, rubbery materials could safely work more closely with people. The problem is that it’s hard to make a soft motor – either it’s really weak and inefficient, or you have to cheat and use hard motors, with only part of the robot soft."
Liquid metals could be the answer. Mercury is the best-known one, but is highly toxic, so Ruddy is working on soft robots using the element gallium, which is liquid above 30 degrees.
“Using magnets and electric currents, we can make liquid metal pumps with no moving parts. We think we can design these to make hydraulic soft robots, like a construction digger but without using intricate machines full of rigid parts.
“We’re hoping to get funding to do this research soon.”
Dr Bryan Ruddy spoke to Jonny Vahry, host of bFM’s Ready Steady Learn show. Listen to the full interview.
Media contact
Nikki Mandow | Research communications
M: 021 174 3142
E: nikki.mandow@auckland.ac.nz