Design for Supply: Linking product development and supply chain functions for assurance of supply
Professor Damian Beil describes how Design for Supply may help firms, especially those in New Zealand, approach supply chain risks.
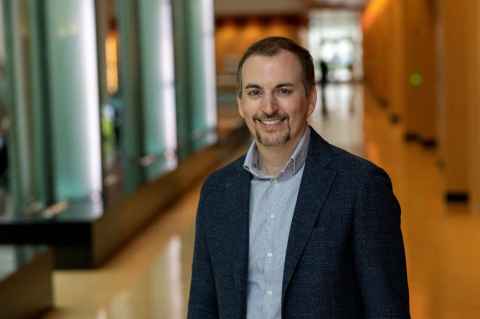
Design for Supply (DfS) is an approach whereby supply risk management is integrated into product development processes. Among the many “Design for X” or “DfX” concepts that have been adopted by companies over the years, design for manufacturing is the most common, having been widely adopted starting in the 1980s as software became available to implement the concepts on a wide scale. Design for supply also dates back to at least the 1980s (before the advent of global supply chains, the emphasis was on purchasing’s role in product development). However, design for supply has not caught on as widely - at least not yet. But that may be about to change, as companies experiencing supply disruptions in the recent past look for new ways to proactively mitigate risks in the future.
If we don’t have a component needed to build a product, we won’t be able to sell it, no matter how good the design is. Supply chain disruptions were massive during the pandemic, and the risks of supply disruptions haven’t gone away and have even increased in the past year, as measured globally by the US Federal Reserve (Global Supply Chain Pressure Index (GSCPI)). New Zealand companies are especially vulnerable given the country’s remote location and dependence on trade, and the risks are particularly acute for companies whose customers are highly sensitive to delay (e.g., specialized healthcare products) or whose products are in highly competitive markets (where customers who switch from one’s product due to shortages may never return).
Product design decisions affect what components are - or aren’t – used in a product, and this in turn impacts the inherent difficulty of maintaining reliable supply of the product. It does not take much imagination to see how supplier geography impacts the product’s exposure to disruptions from ports, shipping lanes, natural disasters, political events, etc. What may be more subtle but equally risky is how decisions to design-in supplier intellectual property or rely on low cost but inherently fragile centralized production can affect a buyer’s ability to obtain supply, by limiting its recourse if the supplier’s production is disrupted.
The “throw it over the fence” approach, whereby designs are simply handed over to supply chain, who are then told to execute, is all too common today. Rethinking this with design for supply isn’t necessarily easy, at least at first. Existing functional siloes and metrics can pose a challenge, if product designers are primarily measured by new product introductions, time to market, and supply chain managers are primarily measured by service levels and costs. Below are a couple of principles which can help companies on their DfS journey.
- Product design decisions cast a long shadow. The design decisions often lock in production, distribution, sales, and repair decisions which will need to be managed throughout the lifetime of the product. It is often much easier, and cheaper, to change design decisions early on rather than ex post.
- Having a conversation between product development and supply chain early on in the product development process is the first step. It gives supply chain an opportunity to weigh in on what potential issues it foresees with the current product design.
After all, a product that cannot be supplied will not be successful, so it is in everyone’s best interests to address such issues. That said, time to market is an important consideration, so it can be wise to facilitate the interactions between supply chain and product development with an interface liaison who acts like a project manager to make sure that deadlines are kept and analysis paralysis is avoided. - Consider the full suite of options to mitigate supply risks. Traditional options to mitigate supply risks for an existing design could range from holding more inventory, to building redundant capacity. However, having the conversation at the product development stage unlocks other options as well. Could the product be designed to use a different, less “risky” component? Or designed in such a way as to not necessitate the use of the component at all (a classic design for manufacturing (DfM) approach)? If we are considering including a supplier’s IP in the product, could we negotiate up-front a way to gain access to this supplier’s IP if the supplier becomes unable to supply (disrupted) or loses interest in supplying the component (changes strategic direction)?; such negotiations are much easier up front, before committing to use the IP. Finally, the homework that is done at this stage to identify risks can also help lay the groundwork for reactive approaches (what we may do once a disruption occurs) if proactive approaches (reducing the chances of disruption or its magnitude/effect through investments, e.g., dual sourcing) are deemed too expensive.
- Prioritize and build a business case. The work described above is not easy, and it can be expensive in personnel resources, investments, and time (especially time to market). Therefore these activities need to focus on the most critical product components. This could be accomplished by high-level leaders on the product development and supply chain sides mutually setting priorities that the rest of their respective organizations will collaborate to address. When a business case is to be presented, try to avoid the temptation to couch the expected costs or
benefits in terms of point estimates. No one knows the exact probability of the next wildfire super disaster, earthquake, or trade war. However, things that might be more easily estimated, like the expected market life of the product being developed, sales and contribution margin at risk, etc. can help provide lower bounds on the cost of disruptions over the product life cycle. This in turn can be used to help reframe the investments needed to mitigate such risks.
Final thoughts
Because the fate of companies rests on having successful products in the marketplace, design for supply conversations can and should be front of mind for companies looking to make long-term advances in how they ready themselves for the future. If the past 5-10 years has taught us what is possible in terms of volatility and uncertainty, surely it is reasonable to expect that the next 5-10 years is likely to bring even more tough lessons. Design for supply can be a way to start planning today for that eventuality.