Hamed Abdoli
Finding additive manufacturing to be one of the most intriguing aspects of his undergraduate studies, Hamed followed his passion for research in the field through pursuing his PhD at the University of Auckland.
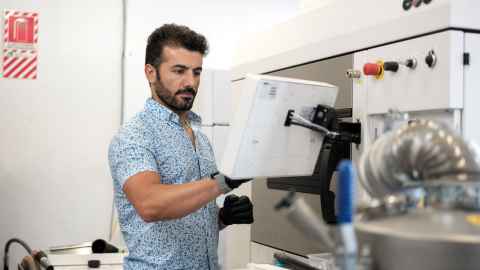
From a young age, Hamed has always been fascinated by mechanisms and how things work. When he began his undergraduate studies, he became very interested in mechanical engineering, particularly in design and manufacturing. This led Hamed to study manufacturing techniques, and as he went on in the field, he found additive manufacturing to be one of the most intriguing aspects of his studies.
“After completing my bachelors and masters degrees in Iran, I decided to complete a second masters degree — the Master of Engineering in Mechanical Engineering at the University of Auckland. Renowned for its excellence in composite material research, the University of Auckland stood as the ideal environment to achieve my aspirations.
“Following a few years of working in industry, I decided to return to the University to study a PhD. My passion for research has always been a driving force in my academic journey. Pursuing a PhD was the natural progression of this; it provided an opportunity for further exploration and deepening my understanding in the field.
“I was fortunate enough to be accepted into the PhD programme through the University of Auckland Doctoral Scholarship. Joining forces with the esteemed research team under the leadership of Professor Simon Bickerton was not only an honour but also a transformative experience for me.
“The focus of my PhD is to develop new techniques to enhance the bonding between a 3D-printed roof beam that has been reinforced by carbon fibres 3D-printed on top of it, in collaboration with the BMW Group.
“When it comes to joining two different materials together, the interface becomes the weakest area. For bonding enhancement, the beam’s surface topology was modified by adding features such as pins and lattice structures to create stronger bonding between the carbon fibre reinforcement layer and the 3D-printed substrate.
“Through my research, I’ve been able to identify and provide a solution which will be implemented in the new generation of cars to allow for a lighter but stronger body frame.
“Since 2022, I have also been working at the Creative Design and Additive Manufacturing (CDAM) Lab as a Research Assistant alongside my doctoral studies. In my role, I’m involved in a wide range of projects. Managing our industrial 3D printers, I oversee tasks for external clients, including partners like Weta Workshop. I also supervise diverse student projects, spanning areas such as food 3D-printing and numerical modelling.
“At the CDAM Lab, we work on utilising additive manufacturing technology to improve efficiency and productivity for people and industries through working on the creative design of objects. There is a wide range of applications for additive manufacturing, including across the healthcare, aerospace, automotive, and marine industries.
“An example of the work we do for the healthcare industry is our creation of a 3D-printed prosthetic hand which aims to improve the quality of life for children with disabilities through its lightweight structural design. We also 3D-print organs, or the area of operation, for surgeons to plan and practice surgery. In addition to this, we have modelled and manufactured a removable, breathable, and lightweight cast for orthopaedics to use as a replacement for plaster casts.
“Within the CDAM Lab, we are also committed to the preservation of Māori culture through utilising our 3D printing services to replicate important heritage items. Recently, we collaborated with the Auckland Museum, employing our scanning capabilities to recreate one of their culturally significant waka artefacts.
“The future of additive manufacturing technology is promising and is poised to transform various industries, shaping a more advanced world. We have recently placed our focus developing hybrid composite manufacturing techniques further, including new techniques to print food — and more specifically for the next stage, meat!”